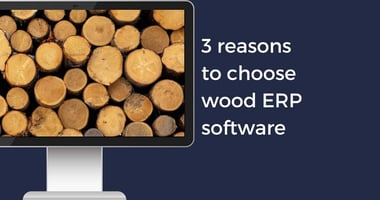
In our case, the investment paid for itself in less than a year. Our tools are flexible, easy to set up and use.
We’ve reduced time lost due to manual and unreliable inventories by 50%. It’s also more precise and easier to access. Production is now organized according to sales and not according to what I have in the yard.
Before inventory forecasts were impossible. I’d go out to the yard every day to count wood and send the information to vendors. I spent weeks out there counting! Since you can’t be in two places at the same time, I was always on the run between the yard and the plant.
Today my forecasts are easier by far and we’re meeting our sales commitments like never before. And the biggest payoff is that I can spend a lot more time in the plant checking production, working with employees, and improving quality.
At the speed we’re moving today, you can’t leave anything to chance. Optimizing your operations is the only way to stay competitive.
Our machines are automated but they don’t interact with each other. Given the volume and the speed we produce each day, there’s no way you can process information like that without it being computerized. Our raw material is ever-changing, never standard, so there’s nothing you can be certain about anymore. We have to rely on our experience and our judgment.
Even when I know that some machines aren’t performing optimally, I’m not sure what to do. For example, if I want to reduce planning losses, I need indicators to show me where the problem is, whether it’s from sawing or drying. By knowing exactly what the key areas for improvement are, I can initiate the right actions.
The data’s there for the taking in the machines but we need a system that collects it, puts it together, and then analyzes and contextualizes it. Using this decision-support tool, we can then make the choices that have the greatest impact on the plant’s profitability.
The installation process in the plant is going really well.
It’s IT so you can’t expect the change to happen overnight. We were able to have the interface adapted the way we wanted, so it’s very basic and speaks to operators and administrators in a way they can easily understand.
Our EFFECTO project manager was on site for each new step to ensure the installation went smoothly and to train user groups.
We decided to have EFFECTO InSite dashboards installed in our sawmill. It’s an essential tool for controlling quality and avoiding slippage. When something unexpected happens, you need to know right away. We lose money on every hour of substandard production.
Automatic monitoring will play an essential factor in saving production going forward.
Customers want precision and quality they can see in every lot, even in the way products are packaged. Wood is getting more and more expensive so we have to do everything possible to save time and money.