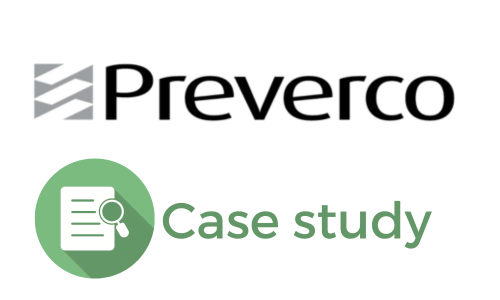
PREVERCO is a Quebec-based manufacturer of high-end parquet flooring. CEO Jean-François Dufresne explains how automated inventory management greatly improved the company’s inventory traceability in real time.
Case study: PREVERCO, Canada, Québec
Just having reliable inventory is no longer enough
We were already very good, but we wanted to be even better
We had an accounting system that managed orders and our finished goods inventory in dollars only, as well as a multitude of Excel files by product and batch. The quality of the information was very good, but the update time was way too long. We were always systematically 24 hours behind where we actually were in real time.
There are a number of stages in the production of PREVERCO flooring. Stages are generally carried out one a time at the rate of one per day. So, in most cases, a 24-hour delay wasn’t really a problem. Now sometimes, of course, there are rush or special orders that we need to get out more quickly and this changes the production timing of the stages and this can create some strange situations. On the production side, for example, the inventory will indicate that we’re behind schedule or that production is only at Stage 1, when in fact, the finished product is already loaded on the truck and being shipped. All because the four production stages were completed on the same day. The inventory hadn’t kept pace...
We needed to improve how we anticipated customer needs
It was also very complicated when it came to anticipating volume deviations in the event of quality problems, wood downgrades, or machine breakdowns. An order for 10,000 square feet could get reduced to 9200 square feet during production without even being noticed before shipment. Suddenly we had to deal with the last-minute stress of not being able to fulfill an order.
Shipments are very often just-in-time because customers only want them when they begin scheduled work on a site. If they don’t get their product in the quantities and qualities expected, we put them in a bad situation. Our capacity to deliver on time is absolutely critical. We must know at every stage of production if we are on target, and if not, we need to be able to adapt, first by notifying the customer, and then by modifying production.